一个企业的持续领先,靠的不仅是对行业需求的深入洞悉,更是看未来的眼界与远见。
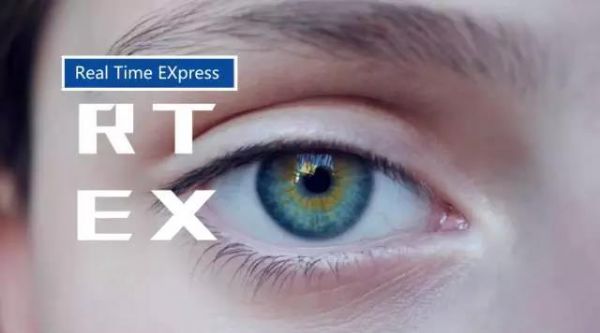
早在十三年前,作为中国具有极高占有率及知名度的伺服电机厂家,松下马达的研发者就预见到了未来将会有一股网络化设备发展的浪潮,于是2004年,RTEX运动控制总线诞生了。
经过多年的迭代和拓展,RTEX像开挂一般从一个襁褓中的产品,成长为一个集IO,步进,变频等下位元件为一体的成熟的工业现场总线,并必将在未来引领工业设备网络化发展的一代潮流。
RTEX(Real Time EXpress), 是松下独有的运动控制总线。开发初衷是实现伺服所要求的高度实时性。
独门绝技:性价比,简单,高可靠性,易开发。
通常的总线产品可分为硬实时和软实时,比如EtherCAT是属于软实时,而RTEX总线则属于硬实时,硬件实时通过硬件来保证通信的实时性和稳定性,和软实时比较,省去了大量软件开发的时间;
要知道软件的开发实际上也不是我们通常认为的是免费及低成本的,软件的开发同样需要很高的开发成本,并且开发门槛较高,通常很多开发者都会最终选择购买成熟的软实时核来完成开发,估算下来并不会比硬件实时便宜,这就是为什么RTEX可以实现超短开发周期,并且实现很高的产品性价比。
当我们的RTEX产品在车间里飞奔创造价值时,软实时总线产品开发还没通过通信连接测试的DEBUG呢,哈哈哈哈哈哈。
以RTEX主站为核心,可以实现RTEX主站与从站之间的高速实时数据交互,通信周期最短可以是0.0625ms,单网段最大32个节点,节点可以包括伺服马达,直线伺服马达,IO,步进马达,变频器等等。
我们当然会有很多场合会应用到超过32个节点的设备,但要知道目前80%的设备,需要的节点数在32节点以下,尤其是在强调柔性生产的今天,设备改造的便利性以及设备快速实现开发设计的要求,使得由一个一个小型设备组成的流水线,更具有快速应变的优势。
同时,32节点以上RTEX就实现不了了吗?非也,RTEX同样可以通过追加CHANNEL(通道)数来实现节点数的倍增,每个通道最后在计算机CPU会师(其实200M主频的MCU就足足够了),实时性不会受到任何影响。
每个节点都有一个输入,一个输出,从而形成数据的单向运行,避免数据冲突和拥塞,保证数据的高速传输。
我们都有经验,高速公路上的车速要比普通国道上要快很多,为什么?
避免了车辆会车,自然不必因为担心前方来车而减低车速。
数据通信同样存在这样的情况,单向传输可以避免数据拥塞,提高车数据传递速度。
RTEX尤其适应于运动控制的应用,所以在伺服马达的控制中,可以进行PP(规划位置),CP(连续位置),CV(连续速度),CT(连续转矩)等等方式的运行。
PP控制通常是点位的控制,发出目标位置坐标来控制位置。常用于点到点,不需要关心行走轨迹的控制方式。
CP控制则需要上位控制器不断进行加减速度,位置的计算,不仅保证最终的位置,同时还要确保到达最终位置的轨迹也和期望的一样。这样的控制方式,可以保证伺服电机的同步运行,从而实现龙门控制等机械上容易因运行速度不一致而导致卡死的现象发生。
RTEX最短到0.0625ms,最高支持2ms通信周期。支持节点数一个通道最大支持32个节点,下位全是伺服的场合可以带32轴伺服马达。
通常对于运动控制最关心的就是同步控制周期,通信周期越小意味着对于轨迹控制的精度越高,实现更高级的轨迹控制。在机床加工上尤其表现在加工效果及精密度的提升。
当然,随着通信周期的缩短,单位时间内运算量增加,对于主控制器的运算要求就会更高。
RTEX是硬件实时是硬件实时,是硬件实时,重要的事情说三遍。
硬件实时的特点就是不需要CPU进行额外的运算,CPU的负担当然降低,所以硬件实时和软件实时的总线,在实现同样的短周期控制时对于CPU的成本要求是不一样的!!!!!!
RTEX适应于各种场景,尤其适应电子实装制造,CNC工作机,机器人及其他娱乐医疗等非标应用行业。
目前由于产业升级发展的需要,以及IOT概念的普及,各类设备都有进化为网络设备的趋势,RTEX从2004年第一代产品推出至今,已经有A4N,A5N,A6N,三代伺服电机产品,经过多年的市场打磨,尤其在半导体,封装贴片设备上获得了巨大的成功,目前是产品的快速上升期,除了前面所述的行业,各类需要高速现场总线进行运动控制的场合,都可以通过RTEX实现。
怎样,RTEX厉害吧!还不赶快跟上组织,参加RTEX CLUB(RTEX伙伴俱乐部),让松下专家和高手手把手带你一起玩转RTEX,进阶跑在行业前沿的技术大牛!
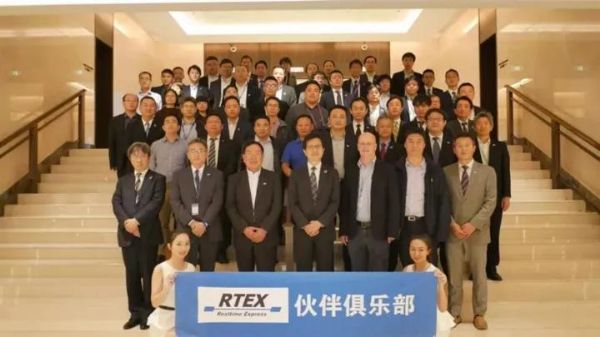